Dura-Bar: Alternative To Steel
Overview
Dura-Bar is an ideal alternative for many steel applications, particularly for carbon steel grades such as 1010, 1018, 1040, 1045, 1141, 1144, 1212, 1214, 1215, 1218, and 12L14. Depending on the application, even some grades of alloy bar are an excellent fit for Dura-Bar.
Many companies are putting Dura-Bar to work in place of traditional steel grades. They are discovering the benefits of continuous cast ductile iron from Dura-Bar. Usually the switch is made because Dura-Bar lowers the cost to produce their part. However, they also realize Dura-Bar doesn't have other issues that plague the steel market, like spot shortages, allocations and fluctuating prices.
Dura-Bar's consistent material performance, distribution network and commitment to customers are unmatched in the industry.
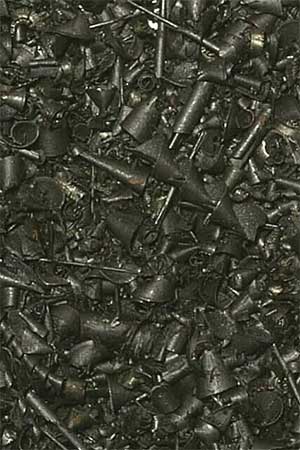
Dura-Bar Chips

Steel Chips
Dura-Bar results in consistent and controllable chip formation, unlike typical steel stringers.
The following chart depicts how the material properties of Dura-Bar 65-45-12 and 80-55-06 ductile iron compare to those of a few common grades of steel.
Material Property Comparison
Material Property | Ductile Iron | Hot Rolled Steel | |||||||
---|---|---|---|---|---|---|---|---|---|
65-45-12 | SSDI | 80-55-06 | 1018 | AISI 1045 JSI 45C | 1117 | 1144 | 12L14 | ||
Tensile Strength (psi) | 65,000 | 75,000 | 80,000 | 58,000 | 81,900 | 58,900 | 102,000 | 57,300 | |
Yeild Strength (psi) | 45,000 | 55,000 | 55,000 | 31,900 | 45,000 | 31,900 | 60,900 | 34,100 | |
Elongation (% in 2") | 12 | 15 | 6 | 25 | 16 | 25 | 21 | 22 | |
Hardness - Average (BHN) | 180 | 198 | 229 | 116 | 163 | 116 | 212 | 121 | |
Shear Strength (psi) | 54,000 | - | 72,000 | 33,060 | 46,680 | 33,060 | 58,140 | 32,660 | |
Compressive Strength (psi) | 110,000 | 59,200 | 115,000 | 58,000 | 81,900 | 58,000 | 102,000 | 57,300 |
Browse example applications and additional advantages below, or request a Steel Alternative Kit—the kit (available as a .pdf via e-mail or packet via snailmail) addresses machinability, heat treating, applications and more.
Example Application: Pulley
Steel's Problems
- Leaded material requires coolant disposal costs
- Poor surface finish
- Poor wear resistance
Solutions and Benefits
- Lead-free Dura-Bar
- Superior surface finish
- Excellent grooving and drilling
- Extended tool life
- Lower shipping cost due to lighter weight of Dura-Bar
Applications
Following are examples of parts which originated as steel, but now made from Dura-Bar have gained significant cost-saving and performance benefits.
Hydraulic Manifold
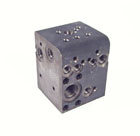
Dura-Bar provided a more machinable material with the needed pressure retention of the application originally manufactured in 1018 steel. The machining cycle time was cut in half and time changing inserts was also reduced.
Compressor Rotor
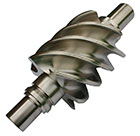
Dura-Bar 65-45-12 properties and superior quality resulted in reduced machining cycle times, lowered tooling costs and improved balance over steel.